4th Newsletter (Workpackage 2: Solar Process Heat, May 2017)
Newsletter WP2 EU Shine April 2017
Welcome to the fourth newsletter of “The Solar Heat Integration Network” (SHINE), which is an initial research training network of 13 PhD students and associated scholarships hosted all over Europe. SHINE PhD projects focus on large solar heating systems for district heating networks and industrial processes, as well as novel components like sorption heat stores and concentrated collectors. Besides research, the network offers a set of specialized and structured PhD courses on solar thermal engineering, sometimes including a limited number of PhD students from outside the network, who can participate in the courses free of charge. The SHINE training network is in its last year and we would like to present some excerpts of our interesting research results on solar heat for industrial applications, including some outreach activities.
Workpackage 2: Solar Process Heat
The majority of the large industries have a high demand for process heat during the entire year. Part of this energy could be provided by solar thermal technology in order to reduce fossil fuel consumption and CO2 emissions. In Central Europe solar thermal energy can provide process heat up to temperatures of 120 °C, whereas the operation temperature might increase up to 200 °C in regions with high direct irradiation.
Due to the EU energy strategy of 2050 and the need to reduce CO2 emissions, the industry's interest in increasing energy efficiency without compromising its competitiveness is growing. Since half of the energy consumption in industry is needed to provide process heat, waste heat recovery and the integration of cleaner heat sources are becoming increasingly relevant. One particular technology well fitted for this task is solar thermal. As a CO2-free heat source, it is an attractive option for supplementary heat generation for industrial, commercial, and as well as for agricultural purposes. Process heat is required year round in most cases, and in months with high solar irradiation (summer), efficiency is significantly increased. This leads to improved returns and a reduced payback period. It also makes the industrial applications’ economics considerably better than those typically found in the residential sector.
The potential for solar process heat utilization depends on the parameters of the selected processes, such as temperature requirements and available solar irradiation at the respective locations (further details in section Process Integration and Collector Technology). In the past few years hundreds solar process heat plants have been installed worldwide. Most of these use conventional flat-plate or vacuum tube collectors, but there are also a few concentrating plants in Switzerland with parabolic trough collectors providing process heat to dairies (section Best Practice Examples).
In contrast to conventional fuel boilers, the upfront investment costs for solar process heat plants are rather high, becoming profitable in the following years, with almost no operating costs. Depending on the country, different subsidies and financial support systems encourage the installation of such plants. In Germany, for example, it is possible to achieve solar heat generation costs of 5 Euro-Cent/kWh for large process heat systems. This makes it a cheaper alternative than fossil fuel (gas, oil), especially when considering future fossil fuel price volatility. There is no volatility is the price of solar heat, the sun is always free. In addition, solar process heat plants are also a reliable energy source with calculable heat cost for at least 20 years, independent of fossil fuels.
In summary, solar process heat is a reliable CO2 free energy source that can be an economically attractive solution for large industries at temperatures below 120°C, which have continuous heat demand especially during the spring, summer, and fall.
Process integration and collector technology
The most suitable applications for solar process heat are processes below 120°C, such as heating raw materials, pasteurization, sterilization and washing, drying, heating of boiler feed water, hot water and steam supply as well as room heating in industrial buildings. A larger list of applications with the associated temperatures is shown in Figure 1.
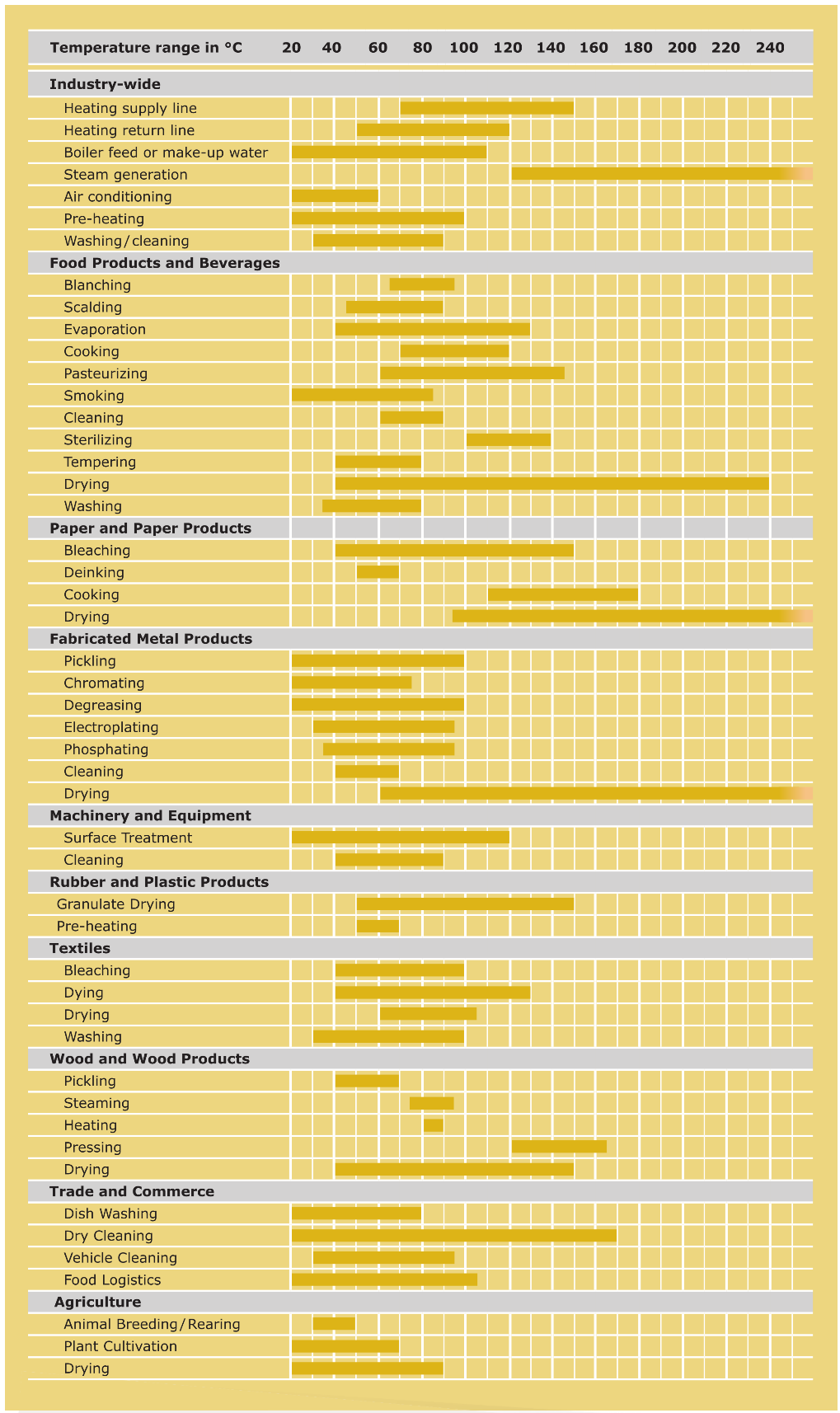
To achieve such temperatures, the current market offers a great variety of different collector technologies, which are both mature and competitive in price. These collectors can be categorized according to the temperature level at which they provide heat (Fig. 2). Heat demand at medium temperatures range from 110 ºC to 250 ºC can be achieved by solar tracking systems, such as small-scale concentrating collectors like Fresnel and Parabolic Trough (well suited for steam generation) or collectors of a completely new design (e.g. CCStaR). For process heat below 110°C conventional, non-tracking collectors can be used, like optimized Flat Plate and Evacuated Tube collectors.
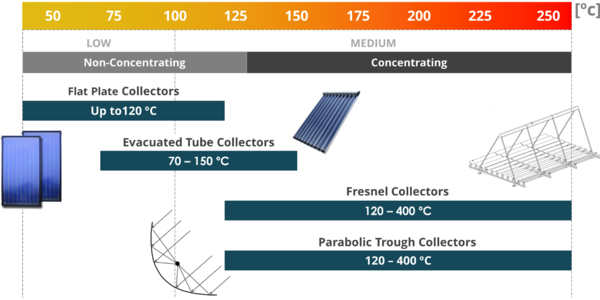
Even though the collector’s output temperature is one of the key parameters for efficiency assessment, it is far from being the only parameter to decide whether a collector is economically viable or not. In fact, the correct choice of collector becomes complicated quickly due to site conditions, labor requirements, and customer needs, which are unique at every potential project site.
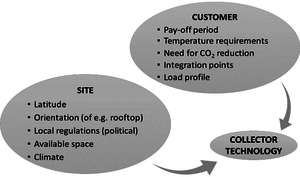
Development of a methodology for the quick assessment and comparison of process heat collectors and systems
PhD Topic, Julian Hertel, Universitat de les Illes Balears
In order to facilitate the integration of solar thermal technologies into industrial processes, research is being conducted leading to notable contributions to standardization, dissemination, and outreach of this field.
In the framework of the PhD thesis, the IAM factorization approach for complex concentrating collector geometries was tested for its validity within the medium to high temperature range. It could be shown that in particular the - -space factorization represented a very accurate approximation for all the analyzed collectors (Fresnel, CCStar, CPC and MaReCo). Furthermore, a sophisticated ray tracing program was developed to make accurate optical simulations of collectors possible. Apart from allowing a greater number of surface reflectance and scattering models, the program is able to run spectral simulations in order to properly analyze new solar materials coated with sophisticated optical thin-films. To date such features cannot be found in any other open-source or in-house ray tracing software. The research supports projects that were initiated as part of expert meetings such as IEA Task 49, SolarPaces Task IV and the STAGE_STE project by EERA.
Best practice examples: Solar Process heat plants
Worldwide more than 500 solar process heat plants exist according to the recent solrico survey with a wide range of solar thermal collector technologies, operating temperatures, plant sizes and locations. Here we present two best practice examples of solar process heats systems in Switzerland, which have been closely monitored for several years by the Institute for Solar Technology (SPF).
According to a recent survey (http://www.solrico.com/en/commercial-solar-heat.html) and on the information provided by the Solar Heat for Industrial Process (SHIP) (www.ship-plants.info) data base, there are 525 plants with a coolector (or mirror) are of at least 416 414 m2 installed wordlwide . The majority of the plants uses Flatplate Collectors, followed by Evacuated Tube, linear focusing and other technologies.
The Institute of Solar Energy Technology (SPF) in Rapperswil (Switzerland) is currently monitoring six different solar process heat plants in Switzerland, three of them using concentrating collector technologies. Here we present two of these plants, which have been closely monitored and evaluated. The plants differ in collector technology, temperature level, and integration concept.
Emmi (Saignelégier)
The first plant is located in Saignelégier, in the northwest of Switzerland at a dairy company. Construction was completed at the end of 2012. The collector field is comprised of 17 concentrating parabolic trough collectors which convert only the direct irradiance of the total solar irradiation into heat, thus requiring a tracking system to follow the sun throughout the day. This collector can easily reach an operational temperature up to 250 °C while remaining fairly efficient. The solar heat from the 627 square meter collector field is integrated into the 102 °C hot water network of the dairy, requiring a collector outlet temperature of 120 °C before passing through a heat exchanger (Fig. 3). If there is no demand the solar energy is delivered to a hot water storage tank, used to support the existing heating system of two oil boilers. The yearly heat demand of the dairy is about 2200 MWh. Measurement analysis shows that up to 11 % (262 MWh) of the yearly required heat has been provided by the solar process heat plant. This reduced the yearly CO2 emissions by 76 tons by displacing some of the burned oil. The solar heating plant efficiency peaked to over 50 % on summer days, correlating very well with the maximum efficiency of 69 % for the single collector under standard testing conditions. The plant is shut down in winter due to snow and low solar availability.
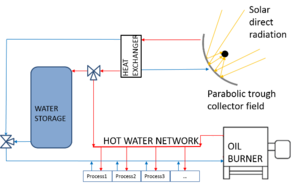
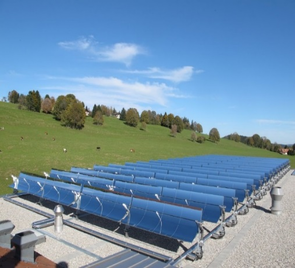
Zehnder (Gränichen)
The second plant is located in the north of Switzerland at a radiator manufacturer company. The plant started to operate in 2012. The collector field consists of non-tracking CPC vacuum tube collectors with an aperture area of 360 m2 and outlet temperatures which vary between 70 °C and 90 °C. The solar heat is used for bath heating of a pretreatment enameling process between 40 °C and 50 °C. The yearly heat demand is about 448 MWh and the solar heat plant provides up to 50 % of the required energy with two gas burners serving as auxiliary heaters, shown in Fig. 4.
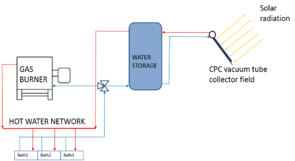
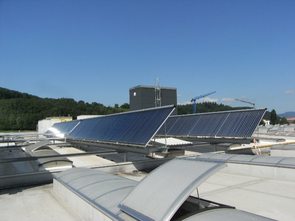
Evaluation, Optimization, Monitoring and Design of Solar Collector Fields for Process Heat at 100 - 200 °C based on Measurement Analysis and Dynamic Simulation
PhD Topic, Jana Möllenkamp, SPF
This PhD focuses on the analysis of solar process heat plants at a temperature range between 100 – 200 °C with the aim of identifying optimization potential and developing guidelines for plant designers.
Existing plants in Switzerland have been monitored and measurement analysis conducted with an evaluation tool developed in Matlab®. Daily, monthly and yearly collector field gains were examined and plant performance was evaluated. Furthermore, specific optical losses (such as row shading, incident angle modifier and end losses) and thermal losses have been analyzed and their impact on the efficiency of the plants examined. For example, row shading losses at a specific parabolic trough collector field reduced the direct irradiation on the collector plane between 10 % in summer and up to 20 % in winter months. This could be reduced by larger row spacing or by changing the tracking axis orientation.
Detailed measurement analysis allowed the identification of several optimization potentials regarding control strategy and system design. One possibility would be to increase the maximum allowed pressure in one of the studied plants to reduce stand still periods, leading to increased thermal output. Changing process intervals or increasing storage size could reduce losses due to excess heat generation at another plant, which would lead to approximately 6 % higher annual yield. Avoiding heat losses at night and during stand still periods by subsequently storing heat with an intermediate storage would increase the total collector field gains significantly (e.g. about 14 % in a 120°C parabolic trough collector field in Saignelégier)
Further optimization potential will be analyzed with dynamic simulation models. Measurements of the monitored plants will be used for their validation. So far, preliminary models have been developed with the simulation tools TRNSYS® and SAM® (System Advisor Model by NREL).
Economic Aspects
Renewable heating represents a promising method to reduce fossil fuel consumption and carbon emissions in the industrial sector. Typical technologies include solar thermal, biomass, geothermal, heat pumps and recently also photovoltaics (providing heat through direct resistance). The optimal type of energy source depends strongly on the local availability of energy and especially on the final price for the consumer. Here we give a short insight into comparison between the costs for solar thermal systems versus photovoltaics and the advantages of energy contracting.
ST vs PV Economic Comparison
Renewable heating is an increasingly interesting method to reduce fossil fuel use and carbon emissions in the industrial sector. Typical technologies include solar thermal, biomass, geothermal, and heat pumps, which are already employed in some lower temperature industries like food and beverage, paper, and textile production. New to the market due to reducing costs are photovoltaics, now being investigated as another technology to provide heat through direct resistance. To determine if photovoltaics can truly produce heat at a lower cost than the other technologies, namely solar thermal, a parametric simulation study was carried out by the University of Kassel. The wide reaching study analyzed numerous collector types, process temperatures (under 150 °C), and locations to determine under which conditions PV heating may be less expensive. Results indicated that at current technology and project costs, solar thermal heating is less expensive in most regions at process temperatures less than 100 °C. PV heating does indicate the potential of producing less expensive heat in colder, cloudier climates when higher temperatures are required. In the future when PV costs are expected to reduce, the regions of lower cost PV heat grow to include much of Europe where temperatures above 80 °C are required. While this can be alarming to the solar thermal industry, PV should mainly be used to offset local electricity demand, as it is typically more expensive than heat, purely a question of opportunity cost economics. Nevertheless, significant efforts must be made towards solar thermal cost reduction to remain competitive in the renewable heat space.
CapEx vs. ESCO
Solar thermal and renewable heating systems have traditionally been financed through a CapEx (Capital Expenditure) model, which means that a company has paid upfront for the technology, waiting multiple years for its payback. While straightforward, it has limited the growth of renewable heating due to longer than desired payback times and resistance from company owners who do not want additional financial risk outside their core business. In recent years, the ESCO (Energy Service Company) model has taken root and seems to be a popular choice. In this model, a project company will install a solar or renewable heating system at the factory at their own cost, including maintenance, then sell the produced energy at an agreed upon price, lower than that of fossil fuels. This is no different than paying your current utility provider monthly for the used electricity, fuel, or water. The ESCO model is popular to industry because they have no upfront expenditure and only pay for the used energy. In addition, this energy comes from a renewable source, like solar, which is inherently immune to the cost fluctuations commonly seen in oil and natural gas. It is a win-win for both the industrial and renewable sector.
The use and optimization of solar and renewable heat to reduce carbon emissions in the food and beverage industry
PhD Topic Steven Meyers, University of Kassel
Food and beverage manufacturing consumes nearly 5% of global end use energy, mostly in the form of heat under 200 °C. Nearly all this heat is still produced by burning fossil fuels, leading to significant CO2 emissions. Energy efficiency can help reduce said emissions by 20..40% but a base demand of heat is still required (ProjectGreenfoods). The remaining emissions can be further reduced and minimized only with renewable heat, primarily coming from solar thermal, photovoltaics, and heat pumps. Technology performance and costs must be considered when determining a preferred path for renewable heat integration which not only robustly addresses the industrial thermal demand but does so at a reasonable cost. Initial results have indicated that solar thermal will play an important role in this process, but will face competition from direct resistance heating photovoltaics in colder and less sunny climates. Solar thermal will also be challenged by industrial heat pumps which can now reach temperatures over 120 °C, though limited by the requirement to have a local waste heat source between 20..50 °C. Together, these technologies can be integrated and controlled in such a way to capitalize on their strengths and support their weaknesses to provide an optimized supply of renewable heat at a reasonable cost. Through this research, clear pathways are being developed to rapidly reduce the fossil fuel use and carbon emissions within the global food and beverage manufacturing sector.
Outreach Activities
COP 22 Experience, S. Meyers (SHINE PhD Student)
As a board member at the International Solar Energy Society (ISES), I was invited to attend COP 22 in Marrakech as part a small delegation of NGOs to represent the role that renewable energy will play to reduce the risk of climate change. I had never been to such a high level event with many powerful attendees like the then US Secretary of State John Kerry, so excited would not fully describe how I felt. Arriving at the event was like nothing I have ever seen. Massive tents covered an area larger than multiple football fields filled with people from every corner of the globe, speaking many languages I couldn’t identify.
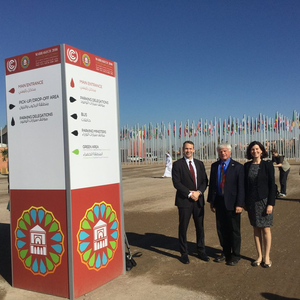
Inside these tents were booths and conference rooms ready to discuss the many topics linked to climate change, including but not limited to agriculture, water, transport, women’s rights, island nations, nuclear power, and fossil fuels. So many connected topics under one roof! One of my tasks was to support the president of ISES, Dave Renné, during his presentation with the REN-Alliance, emphasizing its goal of 100% renewable energy. While challenging, it serves as a target for industry and researchers to strive for to reduce climate uncertainty in an ever changing world. My time at COP 22 was over faster than I expected with nearly every minute filled with discussions of the problem and solutions of the present and future, not to mention some delicious local food of braised lamb in spices. I left Marrakech with a greater understanding of the many interlinked problems of my generation like climate change, starvation, water scarcity, deforestation, and poverty. Through this understanding and experience we can forge a better path forward to tackle these issues, making the world better for generations to come.
Solar Process heat at the e-world energy and water fair in Essen February 2017
In the framework of the EU SHINE project, each work package had the possibility for an outreach activity to present their results. We seized this opportunity to show the potential of solar heat for industrial processes in a different setting than the typical academic conferences which are visited by specialists familiar with the topic. We opted for the e-world fair, which is the leading energy and water-management fair in Europe, to reach out to industrial end users and to present the possibilities of solar process heat. This year 710 exhibitors from the energy and water-management sectors participated and covered a wide range of topics related to energy generation, storage, efficiency and Smart Energy. The exhibition attracted 25 000 visitors from 71 nations. We had a small booth in the area for start-ups and universities where we displayed our posters. As expected, this area was less frequented than other halls and therefore we actively approached interesting companies and visited their booths.

The feedback was generally good and we met with numerous companies such as RWE, BKW, Alpiq, and Viessmann among others. With our visit to the trade fair we could make a small contribution to the dissemination of solar process heat and its benefits to industry.