Quality and Reliability Group
Near-threshold crack extension mechanisms in aluminum alloy EN AW-6082
In the near-threshold regime, cracks may exhibit an unexpected crack extension behavior. This phenomenon is related to the fact that the crack tip field interacting with the microstructure is short-ranged and microstructural features can consequently block or deviate this field completely.
Flat dogbone specimens were cut from rolled blanks of aluminum alloy EN AW-6082 in peak-aged condition (s. Fig. 1). Following mechanical and electrolytic polishing, a part-through notch was cut in the specimen radius using a razor blade polishing technique. Compression pre-cracking was used to introduce an initial crack that is open when unloaded.
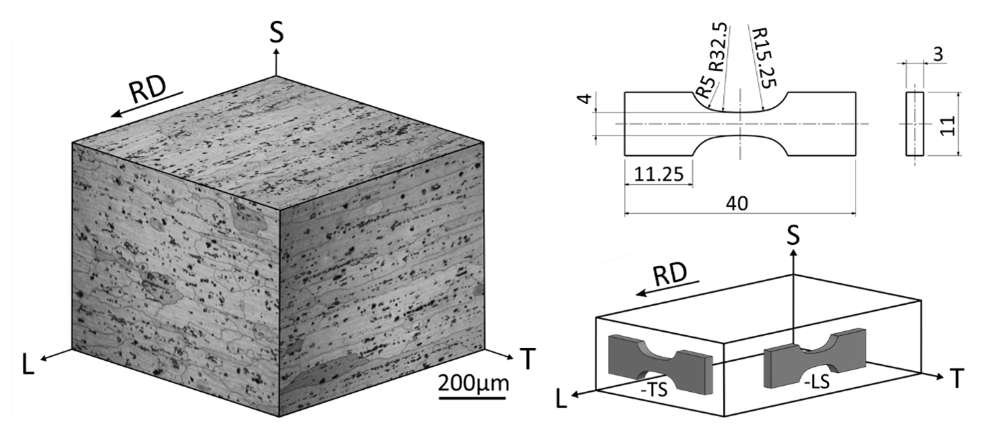
Afterwards, experiments were performed at nominally constant ΔK-values close to the threshold initially determined by continuous load increase. The fractured specimens were analyzed in a SEM (ZEISS Ultra Plus) as well as in a µ-CT (ZEISS Xradia 520 Versa). Moreover, crystal plasticity simulations using the spectral formulation coupled to DAMASK were performed with the aim of getting more in-depth information on the crack extension mechanisms. To this end, digitized models of the experimentally characterized microstructure were generated with the help of EBSD and X-ray tomography. A three-dimensional imaging of the grain structure was realized by wetting the grain boundaries with liquid Ga.
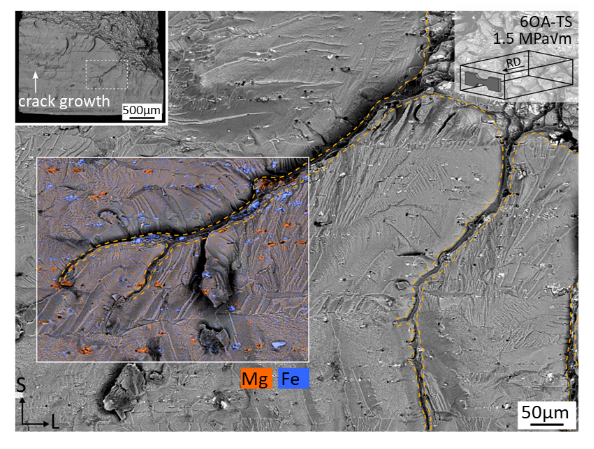
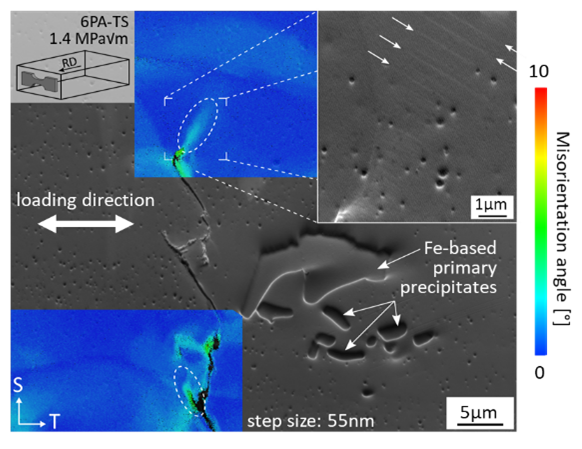
Two mechanisms were identified keeping the crack from continuous extension. First, the crack front was pinned by primary precipitates leading to ductile bridges on the fracture surfaces (Fig. 2). The second mechanism was crack extension in a shear-dominated mode (Fig. 3). This effect was rather pronounced in the case of cracks propagating parallel to the elongated grains and to the lines of primary precipitates which are both related to the rolling texture. Crystal plasticity simulations based on microstructural models of the fractured samples (Fig. 4) show that this effect can be traced back to the multiaxial stress field induced by grain anisotropy and is thus different from the single slip line associated with stage-I microcracks (Fig. 5).
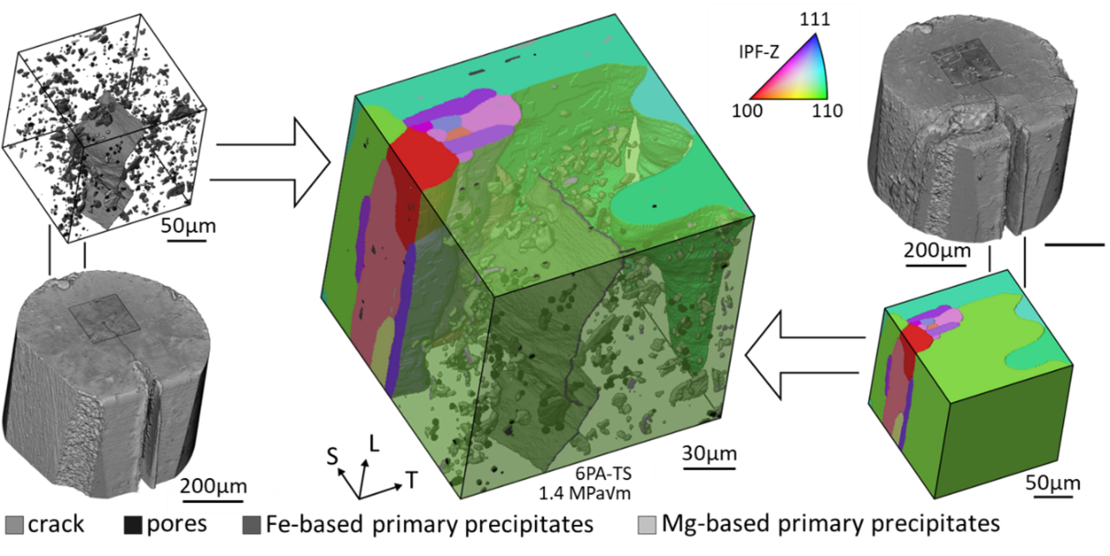

References:
M. Wicke, A. Brückner-Foit, and T. Kirstenet al., Materials Testing, 61, 309-316 (2019)
M. Wicke, A. Brückner-Foit, and T. Kirstenet al., Int. J. Fatigue, 119, 102-111 (2019)
Prof. Dr. Angelika Brückner-Foit
full member
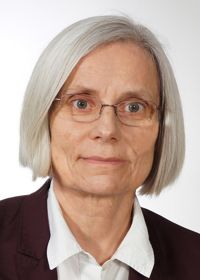
- Telephone
- +49 561 804-3680
- Fax
- +49 561 804-3650
- a.brueckner-foit[at]uni-kassel[dot]de
- Site
- Universität Kassel
Institute for Materials Engineering
Quality and Reliability Group
Mönchebergstrasse 3
34109 Kassel