Meldung
New metal welded joints improve middle ear implants
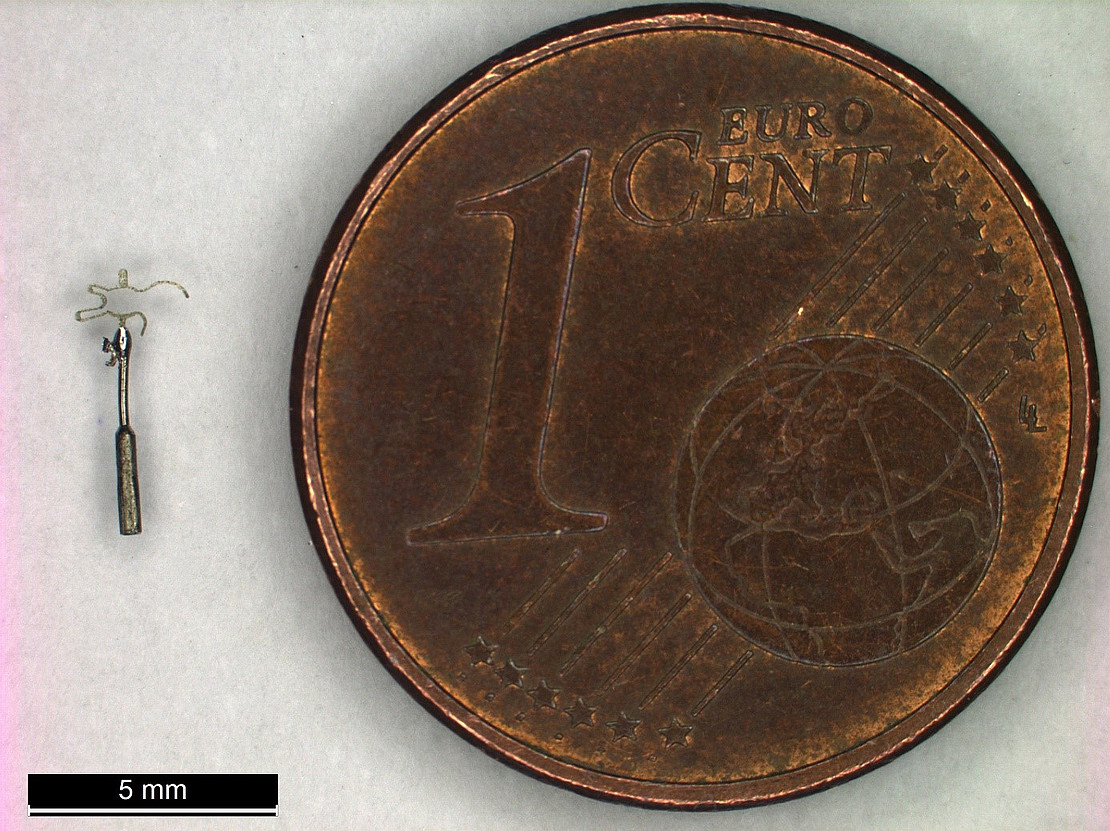
Titanium alloys, nickel-titanium shape memory alloys (NiTi for short) and stainless steels are characterized by excellent corrosion and media resistance, among other things, and are therefore among the most frequently used metals in medical technology. Due to the specific material properties, however, it is desirable for functional, manufacturing and economic reasons to produce so-called dissimilar compounds with other materials and thus combine their advantages in components with customized properties. An exemplary application from the field of medical technology is stapes prostheses, which are used to replace stirrups, the smallest bones in the human body. With a length of 5 mm, a stapes is three times smaller than the diameter of a 1-cent coin.
As part of the research project "MeTiWeld - Intrinsic micro-beam welding of titanium with nitinol and stainless steels for the production of a biocompatible material composite and use of filler materials", which ran from January 2021 to December 2022, the researchers led by Prof. Dr.-Ing. Prof. h.c. Stefan Böhm (Head of the Department of Cutting and Joining Manufacturing Processes) investigated dissimilar beam welded joints in titanium alloys, stainless steels and NiTi using biocompatible filler materials such as niobium, tantalum and hafnium. Both micro-electron beam welding and laser beam welding were used. "When using the filler materials, we were able to achieve outstanding tensile and flexural strength, which significantly exceeded the results of previous studies on dissimilar beam welding of the base materials," explains Michael Wiegand, research associate in the department and head of the project.
The research team also improved a second medical product: using the example of a guide wire required for a cardiac catheter examination, the research team showed that the filler materials niobium or tantalum between stainless steel and NiTi wire, for example, lead to almost twice the tensile strength of the material joints compared to beam welding without filler materials. In the case of the stapes prosthesis, whose stem is made of pure titanium and the coupling element is made of superelastic NiTi, the tensile strength was increased more than threefold by welding in a thin niobium foil. "Our research results also confirm with regard to biocompatibility that the research project has created an essential basis for the transfer to medical technology components," explains Prof. Böhm.
In the MeTiWeld project, the Kassel scientists are working together with the Natural and Medical Sciences Institute at the University of Tübingen/ Reutlingen. The research project was funded by the Federal Ministry for Economic Affairs and Energy and the Arbeitsgemeinschaft industrieller Fördervereinigungen "Otto von Guericke" e.V. with around 400,000 euros.
The University of Kassel focuses its research on molecular components and multifunctional materials. The Institute of Materials Engineering, in turn, is intensively involved with metallic materials. Forward-looking projects with high funding amounts are regularly launched as part of the "BiTWerk - Biological Transformation of Technical Materials" research cluster.
Contact:
Prof. Dr.-Ing. Prof. h.c. Stefan Böhm
University of Kassel
Cutting and Joining Manufacturing Processes
Tel.: 0561 804 3141
E-mail: s.boehm[at]uni-kassel[dot]de