This page contains automatically translated content.
From tree to component: biocomposite material for industry
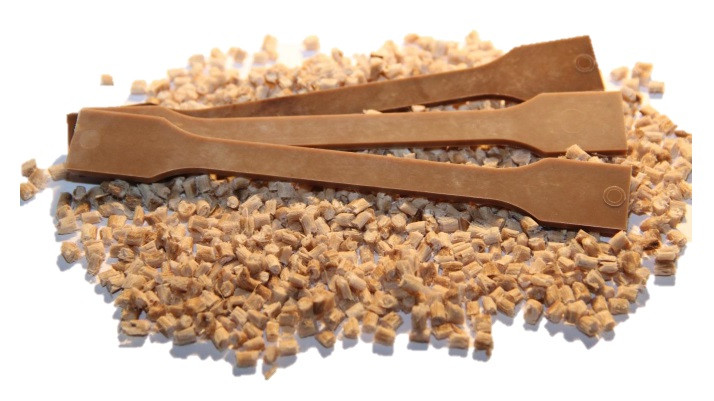
To increase the stiffness of components, the automotive and electrical industries have so far mostly used glass fibers. However, there is great interest in bio-composites that are also suitable for highly stressed components and can replace these glass fibers. In the joint project "Bio-PPT and Bio-PBT with cellulose fiber reinforcement for lightweight construction-oriented use," the University of Kassel and the Fraunhofer Institute for Applied Polymer Research have developed a suitable bio-composite material based on cellulose from fast-growing trees.
Polytrimethylene terephthalate (PPT) and polybutylene terephthalate (PBT) are among the engineering thermoplastics. Instead of fossil raw materials, the researchers focused on renewable raw materials for their new composite. "The basic idea was: we replace the glass fiber with cellulose regenerate fibers, with the effect that the component becomes lighter. Depending on how many fibers we incorporate, the component weighs up to 25 percent less," says Nicole Gemmeke, a research associate at the University of Kassel's Department of Plastics Engineering led by Prof. Hans-Peter Heim. She supervised the project.
The regenerated cellulose fiber is 99 percent cellulose, which is obtained from fast-growing trees. This material is dissolved and chemically processed to produce a homogeneous material that can be further processed. After all, consistent product quality is very important in the industry. A positive side effect is that cellulose fibers have a much lower density than glass fibers, which makes them suitable for lightweight construction.
In their tests, the scientists at the University of Kassel noted the special features of the bio-composite material. "One clear advantage is its notched impact strength," says Gemmeke. The cellulose-regenerated fiber-reinforced Bio-PPT and Bio-PBT composites are up to three times more impact resistant than the glass-fiber-reinforced plastics. So the component would be damaged by impact, but not yet destroyed. "Glass-fiber-reinforced material, on the other hand, breaks with a clear edge in the event of a spontaneous impact," Gemmeke explains.
Additives, such as polyethylene wax or aluminum phosphate, also influence the flow or flame properties of the biocomposite material. As a result, the biocomposite can be used in all areas that have a higher demand on the material than the standard plastic offers.
The joint project was handled by the University of Kassel together with the Fraunhofer Institute for Applied Polymer Research and six companies. It was funded by the German Federal Ministry of Food and Agriculture (BMEL) and the Fachagentur Nachwachsende Rohstoffe e. V. (FNR).
For more information, visit: www.fnr.de under grant numbers 22033714 and 22017415.
Contact:
Nicole Gemmeke M. Sc.
Plastics technology: research associate
Tel.: 0561 804 - 7088
E-mail: nicole.gemmeke[at]uni-kassel[dot]de