This page contains automatically translated content.
Brightest laboratory X-ray source in the world installed at the University of Kassel
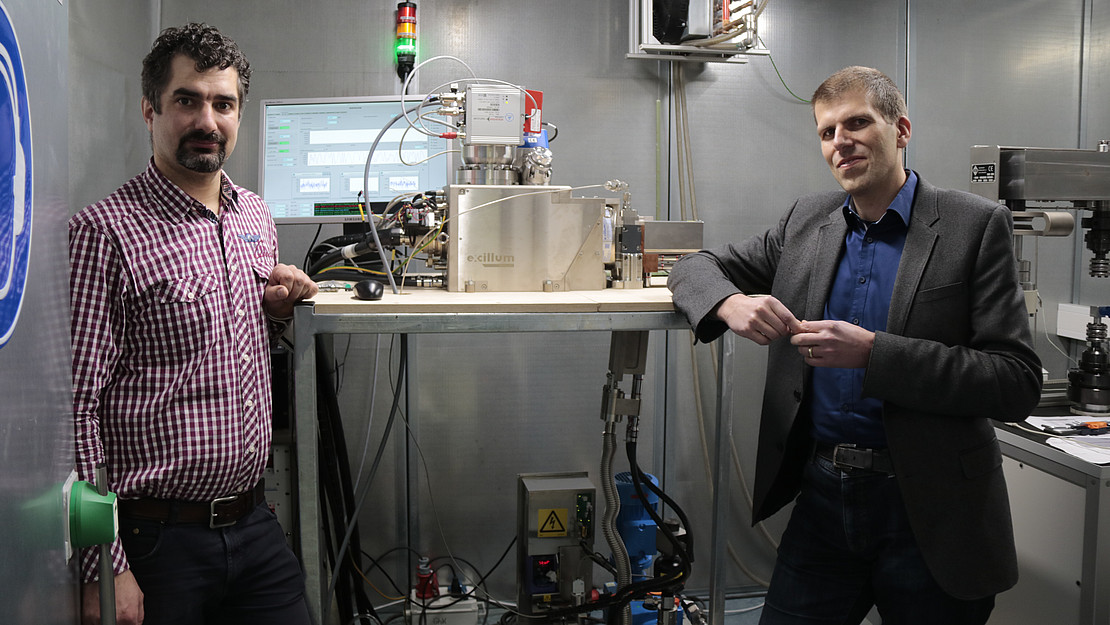
A new X-ray source will further intensify research and development in the field of materials technology at the University of Kassel, opening up entirely new possibilities. With a power of 1000 watts, it generates high-energy and extremely bright X-ray radiation. With this bundled X-ray beam, materials can be X-rayed with the smallest possible resolution of 50 X 50 micrometers. What is special about this is that the required X-rays are generated at a liquid anode made of an indium-gallium alloy, which is hit by accelerated electrons at high speed. A pump continuously circulates the liquid indium-gallium alloy in a circuit system to dissipate the heat generated. These and other special technical solutions allow the high intensity of the radiation and also continuous operation of the facility. "This allows us to observe live what happens in our samples during the experiment, for example how liquid metal solidifies or how components react under compressive or tensile stress, and when exactly the finest microscopic cracks form in the material that we would only see much later with the naked eye," describes Dr.-Ing. Alexander Liehr, head of the X-ray fine structure analysis working group.
Large-scale project: observing 3D printing in real time with X-ray vision
The X-ray source, which cost around 500,000 euros, was funded by the German Research Foundation as part of a major project. In a next step, the high-precision X-ray fine structure analysis will be combined with a unique facility for 3D printing. The new X-ray source will make it possible to observe live at the smallest level in 3D printing how metal layers build up and solidify micrometer by micrometer. "Vast amounts of data are coming into us live: high-resolution radiography and diffraction images from the X-ray source, but also information on the temperature change in the material via other sensors. If we then change parameters such as the exact composition of the materials or process speeds, we can see in real time how the properties also change in 3D printing," explains Prof. Dr.-Ing. Niendorf, head of the Metallic Materials department. This will enable the researchers to develop new materials, make the production of components more sustainable and efficient in the future, improve printing processes, realize higher-performance components and also detect and correct defects more quickly - and all this in metals, plastics and hybrid materials.
In doing so, the researchers in Prof. Dr.-Ing. Niendorf's group will continue to work closely with other disciplines such as manufacturing technology or measurement and control technology as well as working groups in other departments at the University of Kassel. However, existing and new collaborations with other German research institutions and industry will also benefit from the unique new facility at the University of Kassel.
Background: X-ray fine structure analysis at the University of Kassel
X-raying metallic materials: this is done in the X-ray fine structure analysis unit of the Department of Metallic Materials under Prof. Dr.-Ing. Thomas Niendorf at the University of Kassel. They make it possible to analyze materials with micrometer precision, to determine their internal structure, and to determine material properties such as texture and grain sizes. At the same time, it is of utmost importance to determine possible structural defects or to detect residual stresses in the material. In this way, conclusions can be drawn about the mechanical properties of the investigated materials that are central in the real world, for example, in order to increase the service life of the components made from them. With this knowledge, the researchers can specifically adjust manufacturing parameters and optimize the service life of the components. In addition, the research results create further potential for lightweight construction processes.
Contact
Prof. Dr.-Ing. Thomas Niendorf
Head of Department Metallic Materials
Tel.: +49 561 804-7018
E-mail: niendorf[at]uni-kassel[dot]de
Dr.-Ing. Alexander Liehr
Department of Metallic Materials
Head of Residual Stresses and X-Ray Fine Structure Group and Center for Boundary Layer Analysis and Technology (ZerTech)
Tel.: +49 561 804-3645
E-mail: liehr[at]uni-kassel[dot]de
Press contact:
Sebastian Mense
University of Kassel
Communications, Press and Public Relations
Tel.: 0561 804-1961
E-mail: presse[at]uni-kassel[dot]de